GenieCut In-line Window Patcher
Window, Fold and Glue in One Pass
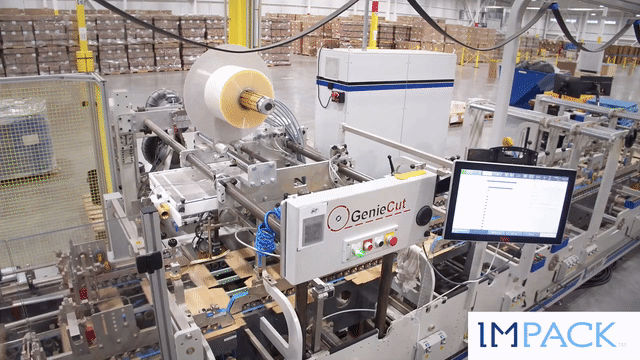
Minimizes Downtime, Optimize Workflow
The GenieCut in-line window patching system for folding cartons integrates directly onto your folder-gluer. The GenieCut is capable of countless window patch widths on straight-line, 4 corner, 6 corner, and crash-lock boxes. The GenieCut can be outfitted with glue systems from the same leading manufacturers that folder-gluer operators are familiar with. The size of the glue applicator module is determined by your production.
Optimizing your folder gluer process and integrating the GenieCut machine can streamline operations and enhance productivity. Most facilities typically operate at an average speed of 100 meters per minute, comparable to one-lane window patching machines. For example, with a medium-sized bakery box, the average production speed is about 20,000 boxes per hour.
GenieCut in action

The GenieCut can window the following types of boxes:
GenieCut Key Features
- Compatible with most box types
- Maximum production speed of 150 meters per minute
- Average production speed of 100 meters per minute
- Offers 5 different widths of glue gun modules
- Can be set up rapidly
- No need for threading and quick to clean
- Patented system designed to minimize downtime
- Integrates directly on your folder-gluer (in-line)
Overview
Innovative Design
The patented GenieCut uses an innovative film cutting system with a stationary knife. Traditional window patchers have servo motors that need to “home” before cycling again, but the GenieCut design allows it to cycle continuously. Moreover, the GenieCut does not come in contact with the boxes, allowing for a scratchless process!
This revolutionary technology increases productivity by reducing downtime. The in-line GenieCut window patching system does not have glue stencils or cylinders that need to be changed or removed for cleaning. The film accumulator (also called a buffer) is operated by vacuum pressure and there is no need to thread the film through a complicated series of rollers and nip points.
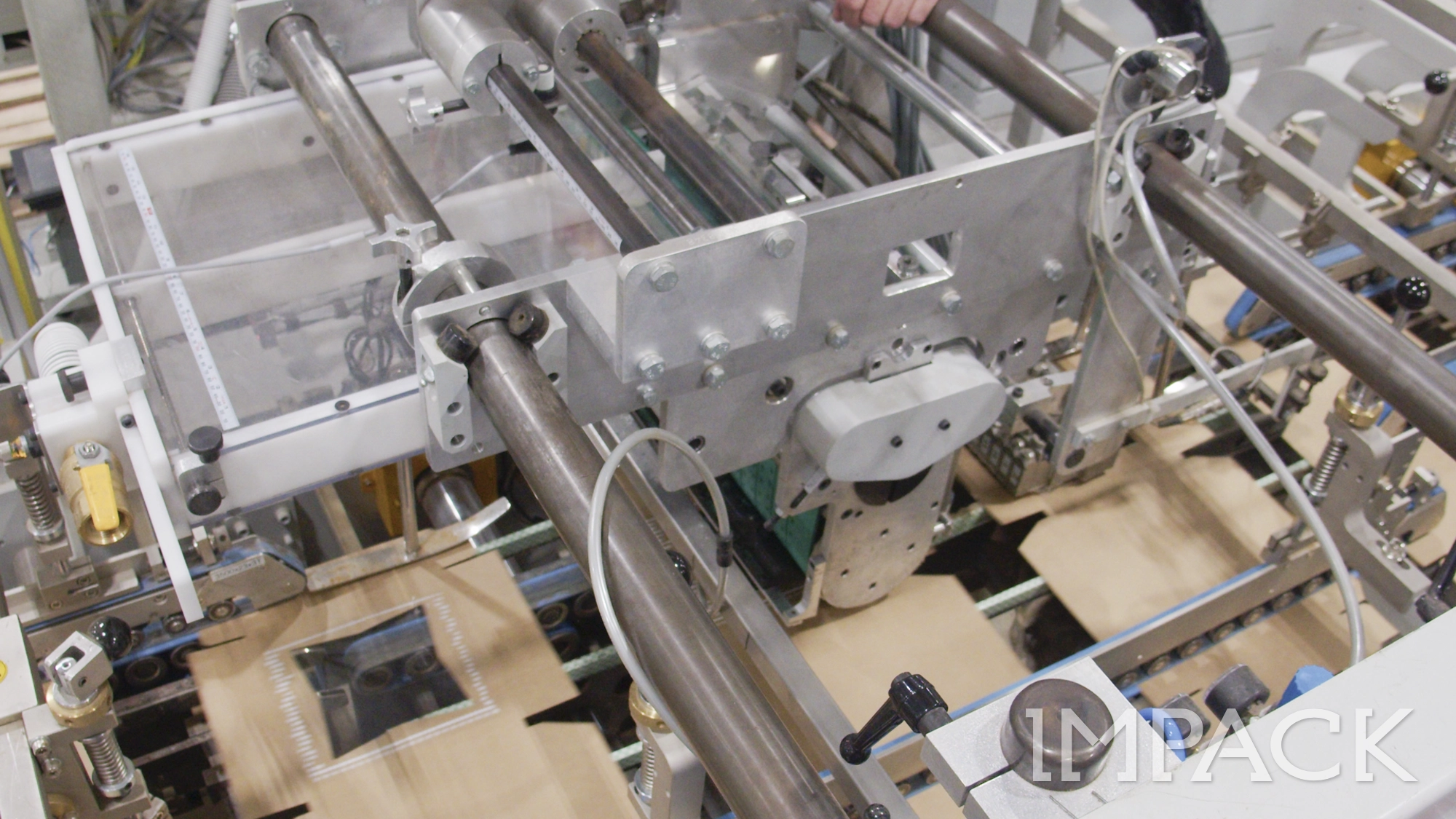
Virtually Zero Additional Footprint
The GenieCut is installed on the folder-gluer machine just before the folding function. Since the GenieCut is integrated onto your current folder-gluer, no additional space is required to add window patching to your production. The mobile frame allows the GenieCut to be easily installed and moved from one folder-gluer machine to another if needed.Additionally, operators can slide the applicator out of the way when not applying windows. Since it does not come in contact with or interfere with the folder-gluer machine operation, the GenieCut can be maintained or prepared for a future windowing batch while the folder-gluer is processing windowless boxes.

Reduced Downtime
With other window applicator systems, window/film misalignment results in significant downtime. It can take up to 20 minutes to clean glue off of the belt and components of other window applicators after an normal production run. With the GenieCut, downtime due to misalignment is a non-issue, since the belt and rollers do not come in contact with the folder gluer or box. After a production run a single wipe with a rag removes any glue residue on the glue gun tip.
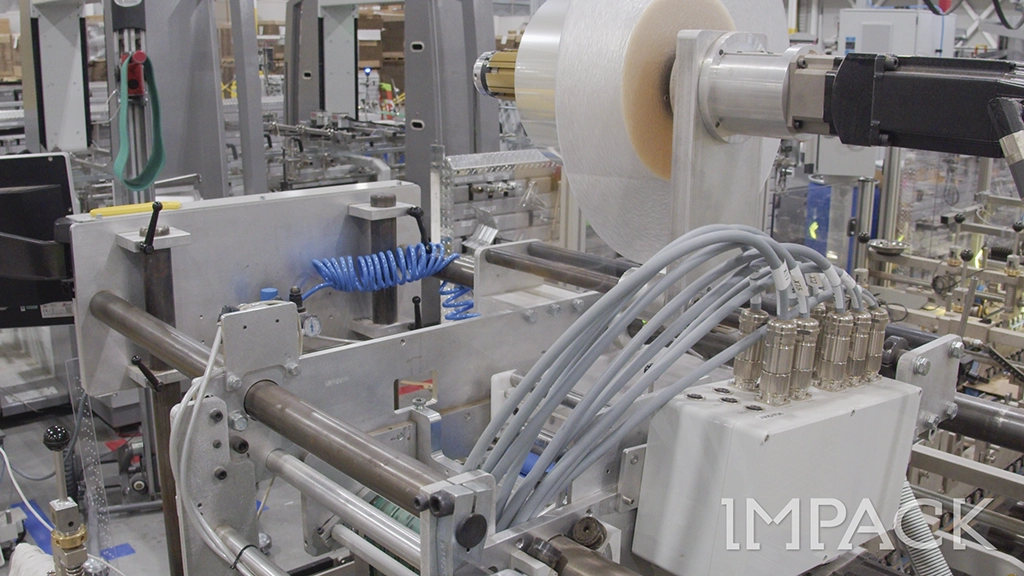
Fast Initial Set-up & Change-over Time
Standard window patchers can take 2 to 4 hours to set up. The GenieCut usually takes less than 15 minutes to set up when recalling an existing job. After initial set-up it’s fast and easy to load additional rolls of film.
The touchscreen controller is user friendly and allows operators to define precise glue patterns. Each dot of glue is 6.2mm center to center. Adjusting the glue volume ensures an unbroken glue pattern once the film patch is placed. Film and glue patterns are stored in the controller reducing machine changeover time from hours to minutes.
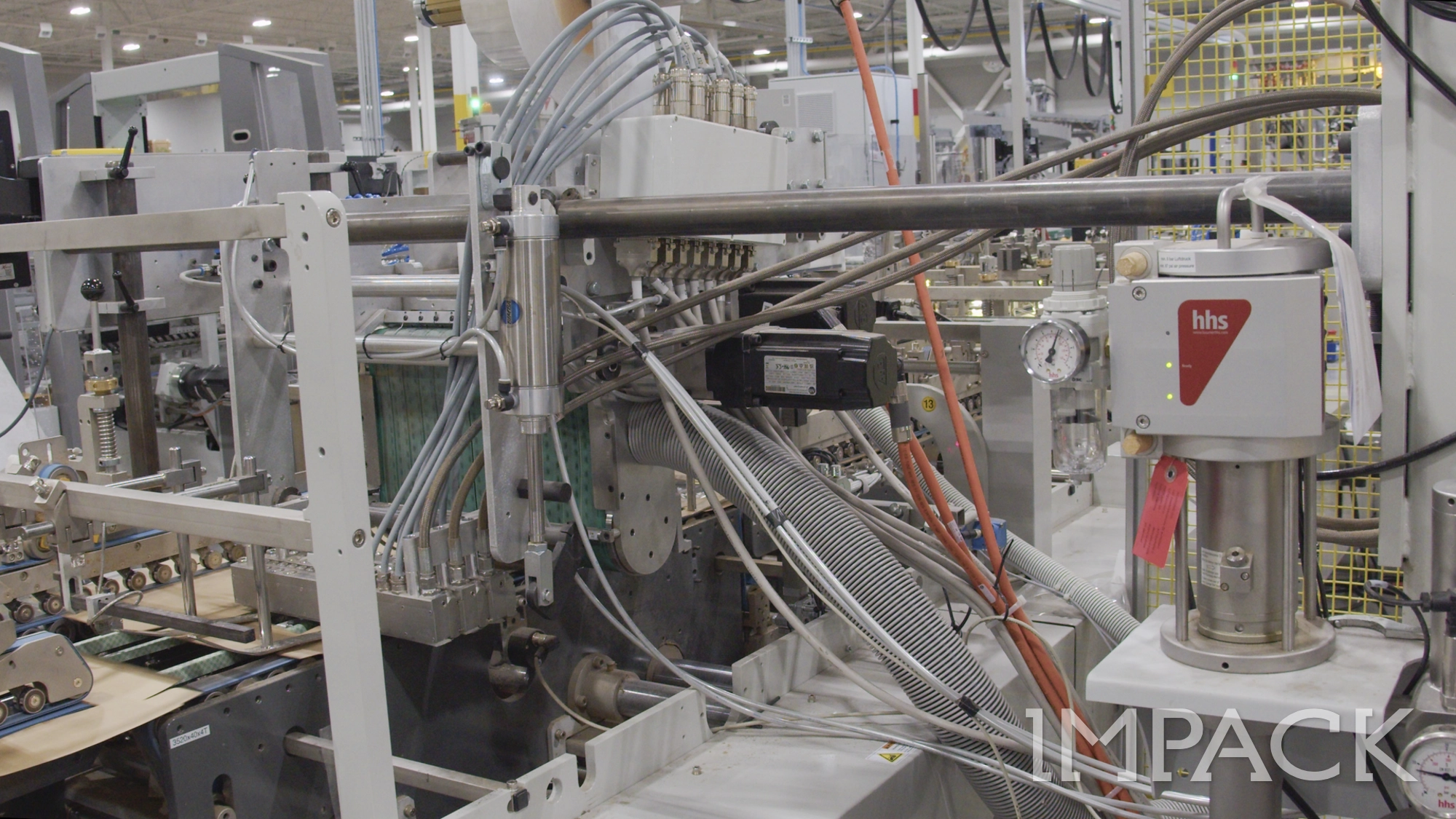
Frequently Asked Questions (FAQ)
-
How long does it take to train an operator?
Operators can be trained in 3-5 days by an IMPACK expert. No prior window machine experience is necessary. If your operators have a basic understanding of glue application systems they have the transferable skills necessary to quickly learn this machine.
-
Will the GenieCut work with the folder-gluer machine we already have?
The answer is usually yes. Our expert advisors will assess the dimensions and configuration of your folder-gluer machine to verify that the GenieCut is compatible.
-
Will the GenieCut work with the glue system we already have?
No, the GenieCut requires a special system capable of feeding the GenieCut’s high number of glue guns.
-
Will we need to purchase the glue system?
The GenieCut incorporates a custom glue system, which is selected according to the customer's preferred brand, and is included as part of the purchase.
The size of the glue gun module has a direct relationship to the size and cost of the glue system, therefore we recommend getting the glue gun module that fits your production needs.
Shortly after the machine is delivered our expert engineers will visit your manufacturing facility, install the machine on your folder-gluer and train your operators. Since the GenieCut system uses glue system technology your folder-gluer operators are familiar with, they quickly become proficient.
-
What film and glue suppliers do you recommend?
The GenieCut requires glue with very specific properties for optimal results. Most glue suppliers can meet these requirements. Our experts will help you select the right film and glue from your supplier.
-
How fast will the GenieCut run?
Optimizing your folder gluer process and integrating the GenieCut machine can streamline operations and enhance productivity. Most facilities typically operate at an average speed of 100 meters per minute, comparable to one-lane window patching machines. For example, with a medium-sized bakery box, the average production speed is about 20,000 boxes per hour.
Dimensions
Categories | Measures | ||
Roll Infeed | Max | diameter |
18 in / 455 mm |
Patch Length | Min | 2.75 in / 70 mm | |
Max | N/A | ||
Patch Width | Min | 1 in / 25 mm | |
Optional |
6, 9,12 in / 150, 225, 300 mm |
||
Speed | Average | 330 FPM / 100 m per minute | |
Foil Thickness | Min | 0.00092 in / 20 μm | |
Max | 0.004 in / 100 μm |
Discover how GenieCut can redefine your workflow.
Reach out today to find out how easy it is to add window patching to your folder-gluer production.